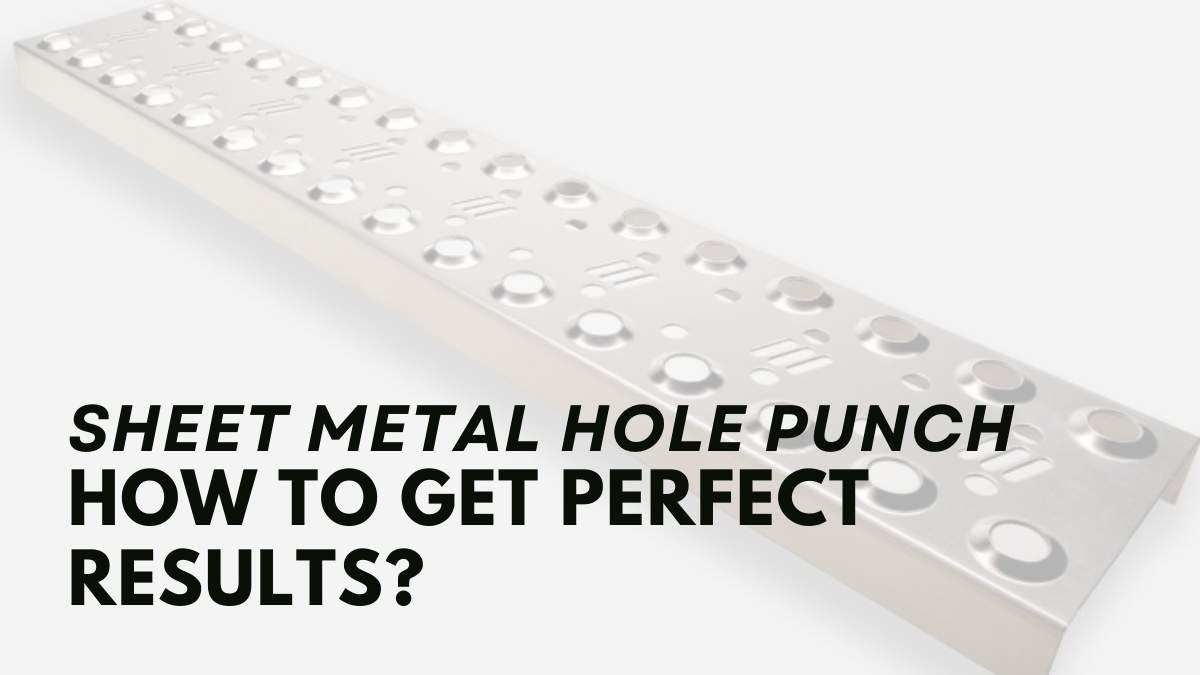
Sheet Metal Punch Hole
Hole punching on sheet metal whether through computer numerical control(CNC) punch presses, fly presses, or power presses follows a similar procedure. The punch forms the diameter of the hole on the top side of the sheet and it will be an exact match to the punch size.
The bottom side of the hole can also formed by the die which is somewhat greater in size than the punch. This difference results in a die clearance, which in turn forms a partly tapered hole. The die clearance is usually a function of the material thickness to be punched, but standard dies are able to punch thin and thick materials. In this article, we will take a glance at the critical and fundamental sheet metal punch hole aspects on a deeper level.
Basics of Sheet Metal Hole Punching
Metal hole punching is a process of punching holes, patterns, shapes, or designs in sheet metal. These punched holes are frequently used for a variety of purposes including assembly, ventilation, drainage, and aesthetics. The procedure is simple and only involves the punch, die and the workpiece. Of course, it is the machinery that does the cutting, but the quality of the operator’s work is critical to achieving the desired result in punching the sheet metal.
How to Make a Hole in Metal Without a Drill?
There are other basic instruments to produce holes in metal not requiring a drill. It’s possible to get clean, accurate holes in sheet metal without having to involve sophisticated tools, by following the methods below:
Using Hole Punch Pliers
Worried about how to punch a hole in metal without having to use a drill? For instance, when you are setting jump rings or inserting decorative holes on metal blanks, hole punch pliers come in handy. These are easy to handle and efficient for small-scale work.
How Hole Punch Pliers Work
The jaws of hole punch pliers have a small pin at their end. When pressure is applied the pin pierces the sheet metal and results in a neat and smooth hole. This tool is very easy to use and can be recommended for those who are just starting with their work or who work on small projects.
How to Achieve Flawless Metal Hole Punches?
The first step to achieving accurate hole punches in sheet metal is to mark the surface with a black pen. It enables you to decide on the location and distances of the holes in order with ease.
To advance precision, maximize the usage of a center punch and a hammer; this creates a small indentation on the metal before employing the pliers. These small indentations will help align the hole puncher and will also guarantee a well-aligned hole punch. When making the hole always ensure that you are punching the hole on the side that you want to face outwards as a way of ensuring that there are no sharp edges visible.
After punching, if there is a sharp or rough edge, gently use a file to smoothen the edges. A round needle file can be used in a forward and twisting motion to try and smooth the inner edges. This step also serves the purpose of cleaning your punched hole for the next step such as buffing or polishing.
Manual Metal Punch Tools
Manual Hole Punching Tool
Hand-operated sheet metal punch tools are perfect for less massive work that does not need much force. These tools are general-purpose and can be used on different kinds of materials such as metal sheets fabric leather and so on. It’s relatively easy to use and convenient for accurate cuts in small applications.
Industrial Metal Hole Punching Machines
In large projects or when large quantities of a particular shape are required for production, hand-held punches cannot suffice. As a result of industrialization, industrial sheet metal punches are indispensable tools for increasing production rates, decreasing the cost of labor, and maximizing time effectiveness. These machines come in either bench mount or free-standing versions and work by mechanical, hydraulic, or pneumatic means. In addition, these machines help cut designs, patterns, and holes. Since CNC technology can easily be programmed, these machines are preferred when it comes to large production.
Hydraulic Metal Punching Machines
Hydraulic Metal Punch Machines
Hydraulic metal punching machines work through the pressure of the fluid. A cylinder with a piston connected to a ram applies this pressure to hit the workpiece; clean holes are made with accuracy. These are sturdy machines typically well-suited to high-production punching applications. Overall, hydraulic punches outperform mechanical and pneumatic machines in terms of punching force, flexibility in working with various metals and their thicknesses, and working conditions characterized by low noise and vibrations.
Precision with Steel Notching
Besides hole punching, the removal of portions from the periphery of a sheet is called notching. Steel notchers are used specifically to put a notch on sheet metal with a view of enabling components to interconnect seamlessly. This process resembles a guillotine cutting action cuts out unwanted material by sandwiching the sheet metal between two blades called shear blades. Metal notching is an important fabrication process that plays an important role in the making of different parts.
DIY Practices for Hole Punching in Metals
When conducting metal punching on your own, several best practices should be followed to ensure efficiency and safety:
- First, it’s necessary to define the size and the form of a hole that is needed. As an added measure of accuracy, draw the locations on paper and then make a final map layout.
- To avoid movement during punching, fix the workpiece properly on the machine or some other jig. Make sure you use adjustable clamps on the workbench when holding the metal so that you can easily adjust them to fit perfectly.
- Select the right size of the punch. For smaller projects, manual punches are preferable since they are accurate and quite easy to handle.
- Appropriate lubrication is important to avoid metal overheating and to achieve good, clean cuts.
- Before proceeding, it’s crucial to check the rate of punches and, if necessary, bring it into conformity with the project.
Cross-Section of Punched Holes
The punched-hole cross-section consists of two parts. The first 25% to 33% of the hole is sheared by the punch and the rest of the hole is drawn by the die, providing a parallel hole section. The remaining 75% to 67% continues to taper, after the die clearance, to make the full hole diameter on the bottom edge of the sheet.
For example, the use of a 5mm punch with a die clearance of 0.2mm gives a 5mm diameter on the punch side and a 5.2mm diameter on the die side. In thicker materials capable of threading, the pilot hole may have to be punched and drilled down to produce a consistent thread size.
Advantages of Sheet Metal Punching for Holes
Sheet metal punch hole offers several key benefits when creating contours:
- It offers an economic way of manufacturing for mid to high-volume production.
- The operation stays cheap, as long as there is no requirement for custom tools.
- The punching process is fast and efficient in its delivery.
- It enables the rapid creation of holes with different shapes and sizes on the working surface.
- Secondary forming operations are normally not required, thus making the process much easier.
- The method can be used with various kinds of metals and tolerances; it has great versatility.
Common Industries That Utilize Sheet Metal Punching
Many sectors require sheet metal service in one form or the other. Punched metal parts are used daily in the automotive, aerospace, electronics, and construction industries. These industries require high precision in the production of their components.
These include aluminum, copper, and titanium, among others are used in the construction of machines. All of these materials entail certain features that define punching characteristics.
In operation, the blows often placed on a material can cause stress and as a result, distortions can happen. It can only stretch, warp, or deform if stress levels increase. That is why sharp tooling is helpful to minimize such problems. Blunt tools cause high-stress gradients and consequent deformation of the material. The coated or treated punches do not allow heat to accumulate on the tools to enhance quality production. Punch quality has a direct relation with the tool sharpness used and the tools last longer.
FAQ’s
Q1. What determines the diameter of a sheet metal punch hole?
The size of a punch used in sheet metal determines the diameter of a punch hole. The punches must be of a size corresponding to the desired hole diameter; die clearances may add to this, on the exit side.
Q2. How does die clearance affect hole punch operations?
A clearance is a space between the punch and the die. Correct breakout is critical to getting a clean hole and the lack of material deformation. Excessive clearance results in big holes as well as poor edge quality.
Q3. What are the benefits of hydraulic sheet metal punch hole machines?
Hydraulic sheet metal punch hole machines are forceful, accurate, and flexible to use and apply to a range of metal thicknesses. They also work with low vibrations and are suitable for mass production.
Q4. How does punch geometry impact metal hole quality?
Punch geometry like shape and angles in which the punch is placed deeply affects the quality of the punched hole. Optimized punches have less burr and provide holes with better accuracy and surface finish.
Q5. What maintenance is essential for sheet metal punch hole tools?
The maintenance aspects involve the sharpening of punches, oiling of the moving parts, and simple checks for signs of wear. For instance, rusty components are vital for the equipment to perform optimally. Maintenance practices provide longer tool durability and a constant diameter of holes to be made during production.